Make to order (MTO), or made to order, is a business production strategy that typically allows consumers to purchase products that are customized to their specifications. It is a manufacturing process in which the production of an item begins only after a confirmed customer order is received. It is also known as mass customization.
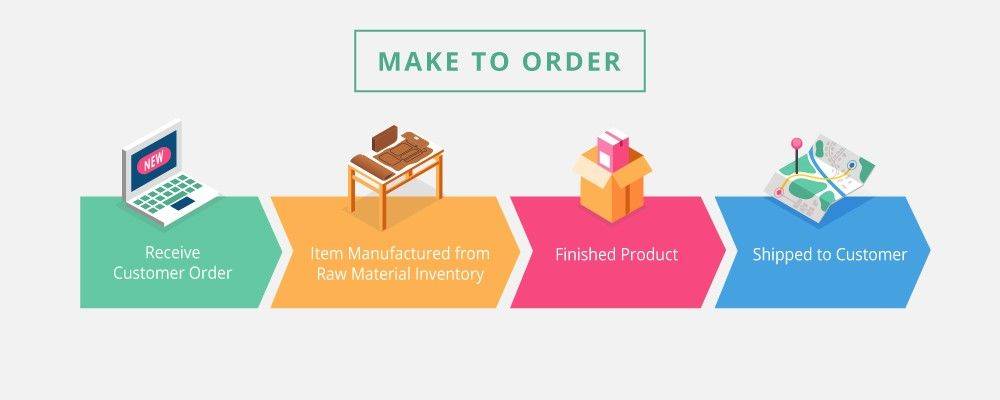
What is Make To Order (MTO)?
Make to Order (MTO) is a production technique in which producers start manufacturing a product only after the customer places an order for it. In such a case, commodities are produced in a customized manner according to the specifications of the customer. The MTO production technique is most suitable for specialized sectors of the industry, such as aircraft manufacturing, construction, etc.
MTO is also referred to as a “Pull Supply Chain” strategy. A pull supply chain strategy is one where the entire process of production, assembly, and distribution of any commodity is driven by actual consumer demand. The process of manufacturing goods starts only once an order is received from the customer, and the number of units produced also depends on the instructions of the customer.
The make-to-order (MTO) strategy means that a firm only manufactures the end product once the customer places the order, creating additional wait time for the consumer to receive the product, but allowing for more flexible customization when compared to purchasing directly from retailers’ shelves.This type of manufacturing strategy is referred to as a pull-type supply chain operation because products are only made when there is firm customer demand. The pull-type production model is employed by the assembly industry where the quantity needed to be produced per product specification is one or only a few. This includes specialized industries such as construction, aircraft and vessel production, bridges, and so on. MTO is also appropriate for highly configured products such as computer servers, automobiles, bicycles, or products that are very expensive to keep inventory.
In order to manage inventory levels and provide an increased level of customization, some companies adopt the make to order production system. The MTO strategy relieves the problems of excess inventory that is common with the traditional make-to-stock strategy. Dell Computers is an example of a business that uses the MTO production strategy, wherein customers can order a fully customized computer online and receive it in a couple of weeks.
Make to Order (MTO) vs. Make to Stock (MTS)
Traditional production methodologies produce products and stock them as inventory until a customer buys them. This is known as make to stock (MTS). However, this system may be prone to wastage and obsolescence, as inventory sits on shelves awaiting purchase. This problem is particularly acute in an industry like technology, where the pace of advancement is quick and the problem of obsolete inventory could quickly arise.
In theory, the MTS method is a great way for a company to prepare for increases and decreases in demand. However, inventory numbers and, therefore, production, are derived by creating future demand forecasts based on past data.There is a high likelihood that the forecasts will be off, even if by just slightly, meaning that a company might be stuck with too much inventory and too little liquidity. This is the main drawback of the MTS method of production. Inaccurate forecasts will lead to losses, stemming from excess inventory or stockouts, and in fast-paced sectors, such as electronics or computer tech, excess inventory can quickly become obsolete.
Advantages of Make To Order
1. Reduces wastage- When a stock of goods lies unsold, there is a wastage not only of the materials used to make them, but also the money and labor put into producing them. In MTO, since products are manufactured after receiving a customer’s order and in the quantity specified, wastage and loss are minimized.
2. Less inefficiency- When a large variety of goods are made on a large-scale basis, there is a risk of inefficiency because workers and machines need to adhere to different rules. In MTO, all efforts are focused on making the product according to the specifications of the customer, so workers and machines tend to be more efficient.
3. Greater variety- Since only customized goods are produced and sold, MTO offers a greater variety of products. In fact, it provides customers the product exactly the way they want it.
Disadvantages of Make To Order
1. Irregular sales- It is difficult to determine when demand may arise for a particular customized product. So, there may be periods of high sales and months of no sale at all. For example, the demand for military aircraft arises in times of hostile international relations, but such situations cannot be predicted in advance.
2. Lengthy delivery time- Since production starts after receiving an order, the product reaches the customer after some time. Moreover, because it takes time to customize the product, the delivery time may take longer.
3. Availability of raw materials- The uncertainty of demand raises the necessity of keeping a sufficient supply of raw materials so that production can start immediately after receiving an order. In case the raw materials are not ready, it takes more time to procure them and deliver the final product to the customer.
Delayed Differentiation
The Make to Order method was introduced to make up for the drawbacks associated with the Make to Stock process. However, MTO was not practical for all commodities. The long delivery times and the added costs associated with customized products restricted the scope of MTO to only a few specialized industries, such as construction and defense goods.
Delayed Differentiation (DD) was developed as a hybrid strategy, combining elements of both MTS and MTO, to be used in industries where the disadvantages of the two methods are apparent. It is carried on in two phases.
In the first phase, as in MTS, a common product base is made to stock. Thereafter, in the second phase, the product base is modified and customized according to the specifications of the buyer as in MTO. The customer takes delivery of the product once it is ready as per their instructions. For example, textile stores sell trousers of the same measurement, but they make necessary alterations to a particular pair of trousers to fit a particular customer before delivering it.
Keeping an inventory of semi-finished goods eliminates the risk associated with wastage and obsolescence of materials. Also, because it takes less time to add finishing touches to the product, the delivery time is shorter. Therefore, with the characteristics of both MTO and MTS methods, DD effectively eliminates all of the other methods’ drawbacks.
FAQs
What is "Make to Order" (MTO)?
Make to Order (MTO) is a manufacturing strategy where products are produced based on specific customer orders rather than being made in advance and stocked. This approach allows businesses to customize products according to individual customer requirements, minimizing inventory costs and reducing the risk of overproduction.
What are the advantages of using a Make to Order approach?
Advantages of Make to Order include reduced inventory carrying costs, minimized risk of overstocking, increased flexibility to accommodate custom orders, better alignment of production with actual demand, and potential for higher customer satisfaction due to personalized products.
How does Make to Order differ from other manufacturing strategies?
Make to Order differs from Make to Stock (MTS) and Make to Assemble (MTA) strategies. MTS involves producing goods based on forecasted demand and stocking them for sale, while MTA involves assembling products from pre-made components based on forecasted demand. MTO, on the other hand, produces goods only when orders are received.
Practice area's of B K Goyal & Co LLP
Income Tax Return Filing | Income Tax Appeal | Income Tax Notice | GST Registration | GST Return Filing | FSSAI Registration | Company Registration | Company Audit | Company Annual Compliance | Income Tax Audit | Nidhi Company Registration| LLP Registration | Accounting in India | NGO Registration | NGO Audit | ESG | BRSR | Private Security Agency | Udyam Registration | Trademark Registration | Copyright Registration | Patent Registration | Import Export Code | Forensic Accounting and Fraud Detection | Section 8 Company | Foreign Company | 80G and 12A Certificate | FCRA Registration |DGGI Cases | Scrutiny Cases | Income Escapement Cases | Search & Seizure | CIT Appeal | ITAT Appeal | Auditors | Internal Audit | Financial Audit | Process Audit | IEC Code | CA Certification | Income Tax Penalty Notice u/s 271(1)(c) | Income Tax Notice u/s 142(1) | Income Tax Notice u/s 144 |Income Tax Notice u/s 148 | Income Tax Demand Notice | Psara License | FCRA Online
Company Registration Services in major cities of India
Company Registration in Jaipur | Company Registration in Delhi | Company Registration in Pune | Company Registration in Hyderabad | Company Registration in Bangalore | Company Registration in Chennai | Company Registration in Kolkata | Company Registration in Mumbai | Company Registration in India | Company Registration in Gurgaon | Company Registration in Noida | Company Registration in lucknow
Complete CA Services
RERA Services
Most read resources
tnreginet |rajssp | jharsewa | picme | pmkisan | webland | bonafide certificate | rent agreement format | tax audit applicability | 7/12 online maharasthra | kerala psc registration | antyodaya saral portal | appointment letter format | 115bac | section 41 of income tax act | GST Search Taxpayer | 194h | section 185 of companies act 2013 | caro 2020 | Challan 280 | itr intimation password | internal audit applicability | preliminiary expenses | mAadhar | e shram card | 194r | ec tamilnadu | 194a of income tax act | 80ddb | aaple sarkar portal | epf activation | scrap business | brsr | section 135 of companies act 2013 | depreciation on computer | section 186 of companies act 2013 | 80ttb | section 115bab | section 115ba | section 148 of income tax act | 80dd | 44ae of Income tax act | west bengal land registration | 194o of income tax act | 270a of income tax act | 80ccc | traces portal | 92e of income tax act | 142(1) of Income Tax Act | 80c of Income Tax Act | Directorate general of GST Intelligence | form 16 | section 164 of companies act | section 194a | section 138 of companies act 2013 | section 133 of companies act 2013 | rtps | patta chitta